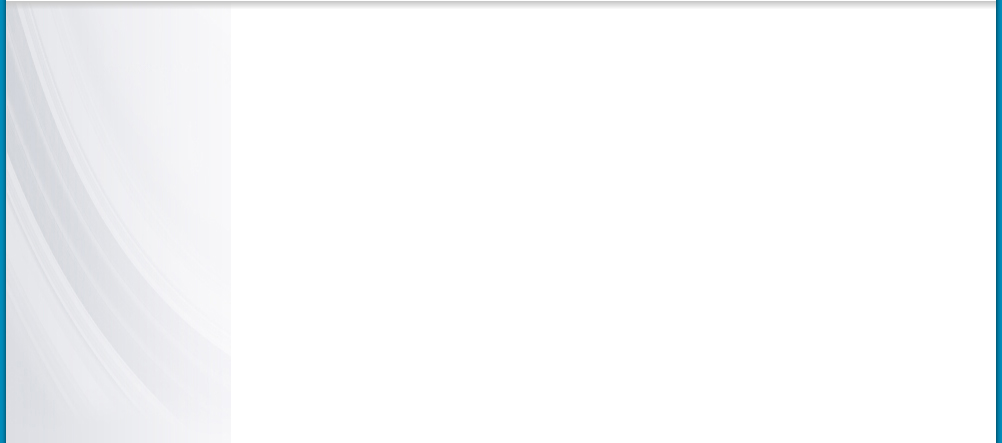
首页“超越娱乐平台超滤技术是膜分离技术的一种,是以0.1~0.5 MPa的压力差为推动力,利用多孔膜的拦截能力,以物理截留的方式,将溶液中的大小不同的物质颗粒分开,从而达到纯化和浓缩、筛分溶液中不同组分的目的。
一般认为超滤是一种筛孔分离过程,在静压差为推动力的作用下,原料液中溶剂和小溶质粒子从高压的料液侧透过膜到低压侧,一般称为滤出液或透过液,而大粒子组分被膜所阻拦,使它们在滤剩液中浓度增大。按照这样的分离机理,超滤膜具有选择性表面层的主要因素是形成具有一定大小和形状的孔,聚合物的化学性质对膜的分离特性影响不大。
UF同RO、NF、MF一样,均属于压力驱动型膜分离技术。超滤主要用于从液相物质中分离大分子化合物(蛋白质,核酸聚合物,淀粉,天然胶,酶等),胶体分散液(粘土,颜料,矿物料,孔液粒子,微生物),乳液(润滑脂-洗涤剂以及油-水乳液)。采用溶质,从而可达到某些含有各种小分子量可溶性溶质和高分子物质(如蛋白质、酶、病毒)等溶液的浓缩、分离、提纯和净化。其操作静压差一般为0.1-0.5MPa,被分离组分的直径大约为0.01-0.1μm,这相当于光学显微镜的分辨极限,一般为分子量大于的大分子和胶体粒子,这种液体的渗透压很小,可以忽略,所用膜常为非对称膜,膜孔径为10-10μm,膜表面有效截留层厚度较小(0.1-10μm),操作压力一般为0.2-0.4MPa(2-4kg/cm),膜的透过速率为0.5-5m/(m·d)。
总之,超滤对去除水中的微粒、胶体、细菌、热原和各种有机物有较好的效果,但它几乎不能截留无机离子。
《多介质过滤器MMF》篇讲到过,我方多介质过滤器产水浊度基本能达到NTU≤0.5,经过袋式过滤器后进入到超滤设备单元进一步过滤。现场共四台超滤设备(其中2台是2015年投用,另外2台是2017年投用),正常情况下是2用2备或3用1备,超滤产水浊度为0-0.1NTU,系统程序设置是运行30分钟反洗一次。记得2016年夏季,由于雨水较少,业主方提供的原水(地表水)水质较差,超滤袋式过滤器每运行约8小时就需要更换一次(滤袋表面附着绿色有机物),且超滤设备运行压力以肉眼可见的速度上升,增加了不少现场员工的工作量。首先,需要及时更换并清洗滤袋,然后在超滤运行压力超过0.12Mpa后需要进行化学清洗(因为污染物多为有机物,所以清洗以碱洗为主,氢氧化钠搭配次氯酸钠)。另外,在夏季(气温超过30℃),超滤和反渗透只要停机超过8小时及以上,均安排当班人员手动反洗一次。特别是超滤,每次手动反洗出来的水偏绿色且有浓烈的异味。
为了确保每一次的化学清洗效果,先用清水(一级RO产水)配少量次氯酸钠进行清洗,整个过程1-2h左右,清洗泵循环即可。冲洗干净后,再用清水(一级RO产水)配氢氧化钠进行清洗,按照循环——浸泡——吹气这三个步骤重复两到三次,然后冲洗干净即可重新投用。若现场条件允许,在用氢氧化钠清洗的过程中,可加入一定量的表面活性剂(例如:三聚磷酸纳、十二烷基苯磺酸钠)。需要注意的是,加入表面活性剂后在清洗的过程中会产生大量泡沫,就像洗衣服一样。这些泡沫在清洗完后需要及时清理,不然泡沫所到之处均是带有异味的污渍。曾经因为这些污渍员工没有及时清理,业主方环保检查时给我方开出罚单。
超滤的化学清洗核心是需要清洗过程中停清洗泵,进行吹气,每次进气约3-5分钟后再停气开清洗泵。当清洗泵重新开启后,很明显能观察到清洗液会变得相当浑浊,说明胶体物质被清洗出来了。另外值得注意的是,设备不管是碱洗还是酸洗,整个清洗过程中需要每半小时手动测一下清洗液的pH,一旦发现pH出现变动,就需要再次补充投加药剂,保证pH一直在规定范围才能保证清洗效果(冬季需要提前给清洗液进行加热,25-30℃最佳)。
为了减轻员工工作量,我方决定在超滤袋式过滤器后补装PP棉滤芯(过滤精度是50微米,100支/台)过滤器,这样即使在每年原水水质最差的情况下,员工也相对轻松。不过由于业主方提供的原水水质实在不敢恭维,我方超滤最好的时候是连续运行7天就需要进行化学清洗,常态是2-4天需要清洗,所以现场运维过程中清洗药剂消耗量很大,与此同时,滤袋和滤芯的频繁更换也是一笔不小的开支。当然,随着气候以及原水水质的变化,滤袋和滤芯的消耗量也在变化。
后面会用另外篇幅继续讲述超滤在极端运行情况下,我方运维过程中遇到的问题和解决方法。(附上我方现场超滤运行参数指标及图纸)