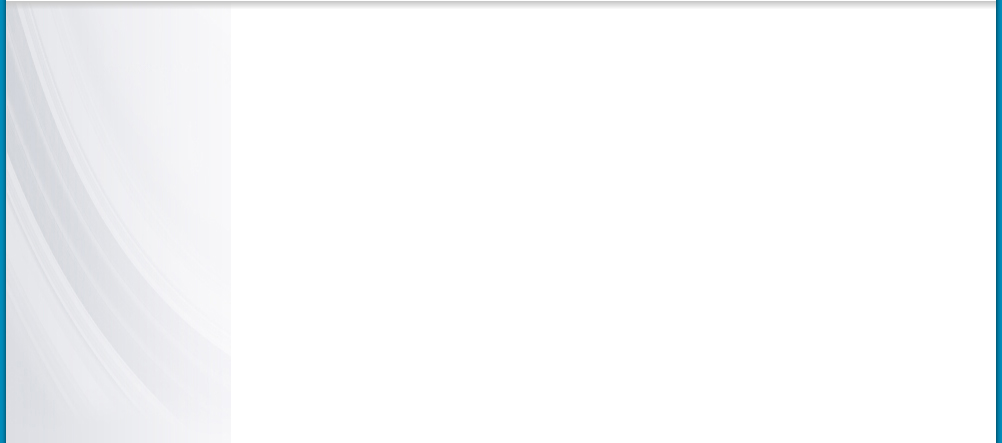
导语:如何才能写好一篇煤化工的工艺流程,这就需要搜集整理更多的资料和文献,欢迎阅读由公务员之家整理的十篇范文,供你借鉴。
在当前的经济发展过程中,对选煤厂的生产要求越来越高,其中节能绿化生产是当前时代背景下选煤厂必须要加以重视的过程,也是选煤厂进行创新发展的方向。选煤厂煤泥水处理系统的工艺流程改造与优化目的是为了降低选煤厂煤泥水的浓度,并且实现洗水平衡,减少传统选煤厂生产过程中的煤泥水排放量。为了实现绿色生产,选煤厂的煤泥水处理工艺改造主要包括四个方面,第一,对选煤工艺进行改造,从而降低煤泥水的浓度;第二,对煤泥水的处理工艺流程进行改造,降低煤泥水浓度;第三,对粗煤泥回收系统进行改造,降低煤泥水浓度;第四,采用先进的脱水技术以及脱水设备降低煤泥水浓度。
本文选取实例对选煤厂煤泥水处理系统的改造与优化过程进行分析。某选煤厂是一座群矿型选煤厂,在生产过程中主要采用主再选跳汰、煤泥水经浓缩后浮选的工艺流程,当原煤进入跳汰机之前会首先经过破碎机预先破碎,产生了很多的次生煤泥量,而且矸石泥化现象十分严重,对煤泥水的处理带来了新的难度。该厂对煤泥水处理工艺的技术进行改造的工艺流程如图1所示:
原来的生产工艺为主再跳汰选-煤泥浮选,经过改造之后成为重介质旋流器分选-煤泥浮选。用重介旋流器代替了跳汰C,将原来的锤式破碎机改为MMD-500型破碎机,由于更新了破碎机,因此次生煤泥量减少,采用重介旋流器之火,中煤和矸石中的煤泥含量相对于采用跳汰机时增加了,使得中煤和矸石的灰分提高,从而提高了分选的效果。另外,还在重介系统中增加了弧形筛和脱介筛,可以使得煤泥水直接进入角锥沉淀池,并且角锥沉淀池入料中的粗煤泥含量也比传统工艺流程中的煤泥量减少,减轻了压缩机的负荷。在煤泥水中加入净水剂,一般40秒左右就可以使得煤泥水变得澄清,而且药剂的用量相对减少,也减少了浓缩机压靶子事故的发生。
改造煤泥水处理系统工艺流程也是选煤厂生产过程中的一个重要途径,通过煤泥水处理系统工艺流程的改造,可以降低煤泥水浓度,有很多选煤厂都采用这种工艺进行生产,减少对环境的污染。对选煤厂煤泥水处理系统进行改造主要包括以下几个方面:
1、将闭路循环系统改为开路循环系统。在传统生产过程中,对煤泥水进行处理时一般都采用闭路循环系统,精煤筛下水通过水力分级设备处理之后,底流通过煤泥筛回收,煤泥筛筛下水再返回到水利分级设备中。为了避免粗煤泥溢出,将煤泥筛和旋流筛的筛板条缝减小,从原来的0.5mm改为0.4mm。
2、利用水介质旋流器降低煤泥筛灰分。在原有的煤泥水处理系统中,粗煤泥可以通过旋流筛和粗煤泥筛进行筛除,然后与经过跳汰机分选之后产生的粗精煤混合起来,进入重介系统再进行分选。我国选煤厂在很长一段时间内都采用这种方式,实践证明这种方法很容易造成重介分选工艺悬浮液中非磁性物含量增多,对悬浮液的稳定性控制不易把握,会降低脱介筛的脱介效果,而且对会最终生产的精煤质量产生影响。针对这个问题,在原来的系统中增加了两直径为500毫米的水介质旋流器对粗煤泥进行分选,旋流器底流通过高频筛回收后再进入混煤系统,再进入离心机进行脱水,最终成为精煤。
经过改造之后的煤泥水处理系统工艺流程如图2所示,在传统的煤泥水处理系统中采用的浮选工艺主要有直接浮选、半直接浮选、浓缩浮选,通过多年实践发现,直接浮选的效果最佳。在煤泥水处理系统改造过程中依旧采用直接浮选方式,将原来的煤泥浓缩机改为尾矿浓缩机,使得尾矿水的处理能力大大提高。而且采用直接浮选工艺流程,还可以使得跳汰系统、重介系统与浮选系统能够实现同步生产,防止某些生产环节的滞后性。
另外,还对集中水仓煤泥水的处理技术进行改造,将原来的改压滤系统滤液和冲洗滤布及清扫用水引入到沉淀池中,经过沉淀池沉淀之后再将其输送到生产系统中,实现对水资源的充分利用。在新系统中还采用了3台GXN-20型高效浓缩机对原来的3台浓缩机进行替换,在原有的2台GPY-200过滤机基础上又安装了一台GP-200过滤机,增加了浮选的通过量,使得浮选工艺流程效率大大提高,降低了精煤中的水分。
经过改造之后的煤泥水处理系统,可以实现对煤泥水的及时处理,降低了精煤中的水分和灰分,实现清水洗煤,洗水浓度也从原来的每升350g降低到每升10g,带来了很大的经济效益和社会效益。
近年来,无烟煤生产是选煤厂生产的重要方向,随着冶金高炉喷吹优质无烟煤技术的不断发展和应用,无烟煤洗精煤的需求量越来越大,而且随着入选力度的降低,传统煤泥水处理系统的工作性能不能满足选煤厂的生产要求,对洗精煤的增产产生了严重的制约。为了对煤泥水生产过程中的问题进行解决,可以进行下面改造:第一,对细煤泥回收系统进行改造,在原来的真空过滤机的位置上增设加压过滤机。第二,增加浮选工艺。随着无烟煤选煤厂煤泥水处理系统的不断完善,在无烟煤生产过程中可以使用炼焦煤选煤厂的煤泥水处理系统工艺,使用加压过滤机进行浮选,从而使得无烟煤选煤厂的煤泥水处理系统工作模式不断创新,实现对煤泥水的综合回收,同时也实现洗水闭路循环,不仅可以确保循环水满足洗选煤的要求,又可以防治煤泥水外排产生环境污染,提高经济效益和生态环境效益。
综上所述,选煤厂是我国煤炭生产过程中的一个重要场所,煤泥水处理系统是选煤厂的主要工艺组成部分,系统的工作性能直接影响选煤工艺流程效果。随着经济发展和环境保护的要求逐渐提高,在选煤厂生产过程中必须要积极加强对煤泥水出系统工艺流程的改造,提高煤泥水处理水平,防止煤泥水随意排放带来环境污染,同时提高选煤厂的精煤质量。
[1] 孙丽梅.选煤厂煤泥水处理系统工艺流程的改造与优化[J].中国矿业,2011(11).
《煤化工》课程是涵盖煤化学、化工原理、反应工程等内容的综合性学科。此门课程通过对煤化工产品开发的生产原理、生产方法、工艺计算、设计、操作条件及主要设备等的介绍,使学生具备煤化工专业的坚实基础,对煤化学工业的原料选择、工艺路线设计优化、典型单元操作及化工工艺的实现有深刻的认识和理解,具备对煤化工工艺流程进行分析、设计、改进及开发新工艺和新产品的能力,从而更好地服务于煤炭行业。淮北市是全国五大煤炭生产基地之一,地质储量100亿吨,远景储量350亿吨。2011年原煤产量达3373万吨,居全国第四位。淮北师范大学(以下简称“我校”)坐落在淮北市,发展煤化工专业有着得天独厚的地理优势。为了满足淮北及周边矿业集团对煤化工专业人才的需要,我校化学与材料科学学院在化学工程与工艺专业开设了《煤化工》专业必修课程。但是,在教学实践中作者发现学生对这门课程的学习疏于对课堂内容的理解和思考、学习兴趣不高。为了充分调动学生积极性和主观能动性,使我校学生在将来的工作岗位上更有竞争力,作者对《煤化工》课程的教学大纲、教学内容安排、教学方法和手段进行了一系列的探索和改革。
由于我校仅开设了煤化工课程,学生对煤化学相关的名词概念不了解,对于教学内容备感生疏。因此,我及时调整教学内容,制定适宜的教学大纲,首先穿插介绍一些煤化学相关内容,包括:煤的生成、煤的结构、煤岩学、煤的物理性质、煤的化学性质等内容。着重强调煤的分子结构理论,探究煤的结构与组成和性质之间的关联性,寻找组成和性质的变化规律。同时在教学中总结煤化学理论与煤化工的相关知识之间的联系,使学生对煤化工的相关知识有了深刻的认识,从而增强了对本课程的兴趣。其次是,对于煤化工课程的重点内容,如:煤焦化、煤的液化和煤的气化,做重点介绍。尤其对工艺原理,流程,以及设备装置的结构特点,结合图片和实例做细致具体讲述,使得学生对煤化工的重点知识有更加深刻的认识。既增加了学生学习的兴趣,又提高了其学习的积极性。
考虑到三年级学生已经完成了对化学基础课程的学习,对于化学理论知识已经有了一定的认知。因此,在教学方法上,我将传统的以教师讲述为主的单一课堂教学模式,转变为讨论式、启发式的新型教学模式,让学生参与到课程的讨论中来。通过布置专业课题或就自己感兴趣的课题,让学生课下查阅相关资料,课上积极参与互动讨论,大胆提出自己的见解,突出学生的主体作用,发挥教师的导向作用,从而调动学生的学习积极性,提高学习效率,促进学生技能的全面提高。同时要强调的是,学生为查阅资料,准备材料花费了不少精力,教师须及时跟踪,认真批阅和讲评,从而提高学生的积极性。
现今,国际煤化工行业发展迅速,许多新技术、新成果不断被应用于生产之中。老的流程工艺逐渐被自动化程度更高的新工艺、新设备所取代。因此,在介绍教材上成熟老工艺流程的同时,要适当穿插与当今煤化学和煤化工发展前沿相关的内容,增加关于当今世界上的最新工艺、设备的讲述,使学生对当今新的工艺流程有更多的认识。因此对于教师而言,仅仅掌握教材上的内容是远远不够的,还需要时时跟踪当今煤化工发展的前沿理论,更好地充实自身理论水平,这样才能更好地激发学生学习的兴趣。另外,由于《煤化工》具有实践性较强的特点,教学过程中必须注意理论联系实际,把教学和实际生产过程有效结合起来,使学生既能在实践中加深对书本知识的理解,又能提高动脑、动手的能力。为此,根据学校周边厂矿企业生产实际,我们走访焦化厂,了解其生产工艺(备煤工艺,炼焦工艺,化产工艺,甲醇工艺,干熄焦工艺),并将具体生产工艺流程的相关知识增加到教学活动中,理论联系实际,使学生对实际工业生产有了更深刻的认知。既增加了学生的学习兴趣,又使学生对企业的生产流程有了更加清晰的认识,得到了用人单位的一致好评。
煤化工课程内容涉及大量的设备图和工艺流程图,采用常规的板书,在黑板上画流程图耗时耗力,不能满足现代化教学的需要。此外,板书绘制的流程图为二维平面图,学生对设备构件的立体构型、工艺流程中原料和产品流向等没有完整的概念。学生理解起来非常吃力,教师讲授过程同样费力。引入多媒体教学可以有效地解决上述问题,实现教学目的。借助多媒体辅助教学软件,开发了煤化工多媒体辅助教学课件,尤其是工艺原理图、设备示意图,可以借助专业绘图软件直观、形象地向学生展现,可以帮助学生理解复杂的装置立体结构和工艺流程图,增加学生的学习兴趣及理解程度。此外,借助于网络上丰富的教学资源来充实课堂教学内容,在教学过程中根据具体需要,及时地向学生介绍国内外最新的煤化工生产工艺流程和技术等,并对国内外知名煤化工企业的最新动态、发展趋势需求等进行信息传递,使学生不仅加强和巩固了理论知识,增加了学习的积极性和主动性,而且提高了学生再就业环节中的适应能力和解决实际问题的能力,从而更好地服务于企业和社会。
总之,通过激发学生的学习兴趣、调整教学内容、结合煤化工研究的前沿理论、传统教学与多媒体教学相结合,能提高煤化工教学的质量,满足经济日益发展对创新型人才的需求。教师要想取得更好的教学效果,就要有创新意识和科研进取精神,不断完善教学内容,调整教学方式更好地为学生服务,提高教学质量。
[1]张香兰,王启宝.《煤化工工艺学》教学中问题启发式教学方法初探[J].化工时刊,2011,25(10):64.
[2]沈扑.《煤化工工艺学》课程的教改实践与探索[J].新课程研究,2010,177:37.
在我国能源消费结构中,煤炭作为主要能源的格局短时间内不会改变。随着可持续发展战略的实施,人类越来越重视保护生态环境和节约能源。而对煤炭行业也是如此也向我们提出了新的挑战和要求,那就是大力发展洗选工艺,走煤炭综合利用、能源清洁生产的道路。随着我国洁净煤技术发展战略的实施,我国的原煤入选比例逐年提高,目前原煤入选量已达到11亿t,约占原煤生产总量的43%以上。重介质选煤方法脱颖而出,它以分选效率高、对煤质适应强、可实现低密度分选、操作方便、容易实现自动化的优点,深受到选煤业的重视。
煤炭洗选利用是煤炭生产和综合利用的重要环节,是实现煤炭清洁生产、节能减排、可持续发展的前提条件。我国从事重介质选煤技术的研究起步于20世纪50年代中期,“十五”期间,在政策引导和市场拉动下,我国的重介质旋流器选煤技术发展迅速,开发了具有自主知识产权的新工艺、新设备,为重介质选煤技术的推广应用和煤炭企业经济效益的提升作出了贡献。近年来,我国重介质选煤技术创新在简化工艺系统、设备大型化、提高重介质旋流器人料上限、降低有效分选下限以及生产过程自动控制等方面取得了突破性成就,重介质选煤工艺流程也越来越简化,采用一套介质回收净化系统,实现了100~0mm原煤分级入选。目前,我国已经掌握了重介质选煤技术,能自行设计大中型重介质选煤工艺的选煤厂。尤其是在重介质旋流器选煤技术方面,自主研制开发了一系列大直径的三产品重介旋流器,某些技术和指标已经达到或者超过世界领先水平。为生产现场广泛采用重介质选煤法,降低基本建设投资和生产费用,迅速提升我国重介质选煤入选比例,促进了重介质选煤技术的推广应用,提升了煤炭企业的经济效益、社会效益和环境效益起到了重要作用。
为了满足煤炭需求的增加,解决原煤质量贫、细、杂的现状,当前选煤设备的研制开发,主要朝着增大设备处理能力、提高分选效率的方向发展。根据分选原理的不同,重介质选煤设备主要分为两类:第一类是重介分选机,是在重力场中分选;第二类是重介质旋流器,是在离心力场中分选。
我国已经研制出双锥形重介分选机、斜轮重介分选机、立轮重介分选机。斜轮重介分选机是由分选槽、斜提升轮、六角轮、传动装置等部件组成,其优点有:分选效率高;悬浮液的循环量少,密度比较稳定;分选粒度范围宽,上限可达1000mm。立轮重介分选机的分选机理与斜轮分选机基本相同,不同的地方是:立轮分选机的提升轮垂直安装在分选槽内,分选时采用水平流和下降流,即合格悬浮液从给料端以水平方式给人分选机,在分选槽底部的排料闸门排出部分悬浮液。立轮分选机具有布置紧凑、传动简单、提升轮耐磨损、维修量小、占地面积小、制造容易等优点[2]。实践经验表明:重介分选机具有分选精度高、分选效果好、分选粒度范围宽、处理量大等优点,适用于块煤的主、再选和排矸作业。
我国从1965年开始研制开发重介旋流器,重点是扩大旋流器的入料上限和降低分选下限。多年来,经科研人员的努力,现在旋流器的人料上限已经达到50mm,分选下限已降到0.04—0.05mm,基本实现50~0mm不脱泥全部入洗。重介质旋流器选煤的优点:分选粒度范围宽,分选效率高,工艺流程简单,投资少,操作方便,容易实现自动化,处理能力大等同。
人选原料煤粒度及产品结构不同,重介质选煤工艺有多种,分选效果也各不相同。以下介绍了三种选煤行业中种目前应用较成功的重介质选煤工艺流程。
20世纪90年代,我国设计的兴隆庄选煤厂、桃山选煤厂、盘北选煤厂、北岗选煤厂等采用该工艺流程;该工艺适合于原煤可选性好,用跳汰方法可以实现分选的选煤厂。优点是采用跳汰机预先排矸,可以降低矸石对重介质旋流器分选效果的影响,减少重介质分选的入料量和旋流器的磨损,且精煤产品质量高;缺点是工艺流程复杂,设备种类台数多,中煤里损失一部分精煤因此精煤产率低。
两产品重介质旋流器分选工艺流程是重介质分选工艺的基本形式,先用低密度旋流器分选出精煤与重产物,然后再将重产物送人高密度旋流器分选出中煤和矸石。此工艺主要应用于原煤可选性较好、中煤含量较低及要求精煤灰分较高(如动力煤)的原煤分选。因为各厂普遍存在中煤,所以两产品重介质旋流器分选工艺在实际生产中应用较少。此外,该工艺介质回收流程较复杂,管理不方便。
三产品重介旋流器是由一台圆柱旋流器和一台圆锥旋流器串联组成。第一段为主选,采用低密度悬浮液分选,选出精煤和再选人料,同时由于悬浮液的浓缩作用,为第二段准备了高密度悬浮液。第二段再选,分选出中煤和矸石。该工艺可用单一低密度重悬浮液一次分选出精煤、中煤、矸石三种产品,节省了一套高密度重悬浮液的制备、输送、回收系统,简化了工艺流程,减少了设备台数,节省厂房空间,便于生产管理。该工艺有两种形式,即有压给料和无压给料三产品重介质旋流器分选工艺。无压给料分选工艺以其流程简单、操作方便、基建投资低等优点,被新建厂或改造厂普遍看好,并得到推广应用。目前采用该工艺的选煤厂总设计能力超150Mt/a,约占我国选煤能力的20%以上,并成为我国选煤厂主要的选煤工艺并推广使用;缺点是采用三产品重介质旋流器分选虽然可以降低基建投资和运行成本,该工艺对中煤密度的调节比较困难。
选煤厂选煤技术设计是选煤厂设计的核心,选煤设计是否先进直接决定选煤厂在设计上水平的高低。近几年随着我国煤矿行业的快速发展,大批新技术、新设备得以不断更新,因而尽快优化资源配置强化工艺设计的合理性,对煤炭的洗选及加工而言就变得日趋重要。
近些年来,我国在选煤技术方面的发展速度很快。在20年前,我国选煤技术上还是以跳汰选煤法为主,近些年来,我国的选煤方法已经愈趋向于多样化,包括重介质选煤、浮选以及风选等等,其中,重介质选煤技术是我国现今应用最多的技术。但是,由于我国选煤厂规模不大、选煤入选率较低,导致我国现如今的选煤技术与先进国家的技术存在着较大差距。
与国内选煤工艺落后阶段比较,近几年以来,我国的选煤量已经靠近发达国家的标准,同时正处于一个快速发展进步的阶段,然而,在总体上看,我国煤碳市场仍处于一个供小于求的阶段,这对选煤厂选煤技术发展提出了更高的要求。
虽然说我国煤炭入选量已经得到了进一步的提升,但就原煤入选率方面来看,仍然未能与其他国家相提并论。较低的原煤入选率不仅会直接致使煤炭品质的下降,而且在生产过程中还会产生硫化物,对周围环境造成严重的污染。
随着国内煤碳市场以及有关选煤设备的不断进步和发展,在选煤厂的设计上逐渐趋向自动化和简洁化。选煤技术工艺的设计是否合理、简洁已成为判断选煤技术水平的重要依据。而在设计上是有一些特点的。首先在确定选煤方法后,才可以进行工艺的设计,设计时,要充分结合各种因素使各环节设计得以细化,各环节都可影响到选煤厂管理水平、经济效益,同时也可以直接反映出选煤工艺特点。例如原煤排矸环节、煤泥分级和分选环节、煤泥水处理环节,这几个环节通常都需要按照煤质实际情况和厂内设备及现场情况等方面优化设计,但这是可以调整改变的。
20 世纪90 年代以来,我国选煤厂选煤技术主要以跳汰选为主,稳定的跳汰机构性能和成熟的跳汰工艺对我国选煤技术的发展具有非常重要的作用,同时也积累了丰富的生产管理经验。但重介质旋流器的出现迅速成为我国当时的主流选煤技术。在2000 年左右,我国选煤技术迎来了第一个高峰期,一方面,用户不断提高的产品要求以及过度开采加大了煤炭可选性难度;另一方面,新型高效率设备如重介质旋流器研发成功,这些原因导致我国出现了大量的选煤厂扩建或新建选煤厂。
我国的煤炭资源较为丰富,但是由于市场上需求变化,使得原煤的性质有所不同,所以统一的技术不能够很好地适应需求的变化及原煤的性质要求。选煤工艺的多元化有利于按照市场的需求及原煤的性质对选煤技术做出调整,从而提高选煤生产效率。在选煤厂的设计上要根据地区煤矿情况,选择合理的工艺。目前选煤工艺主要有重介选和跳汰选两种。一般以最直接、最简单、最有效作为基本选择原则。
重介旋流器分选利用的是原煤离心力进行分选,一般用在难选的末煤或原煤。由于煤炭市场对产品的要求不断提高且煤层的结构越来越复杂,这对选煤的工艺要求也在不断提高,重介旋流器可以很好地对这些问题予以解决,因此得到了广泛的应用。
传统选煤的工艺是跳汰选,其无法实现高精度的原煤分选,但对易选煤分选的精度很高,因此成为易选煤洗选的重要工艺。
高效选煤工艺的另一个特色就是其产煤系统的实用性和灵活性。但是选煤厂为提升效益,要及时地根据煤炭市场的需求对生产计划进行调整,从而在激烈的市场竞争中得以生存和发展。高效的选煤厂要按照用户的需求进行量体裁衣,对于设备的选择应合理,并不断优化工艺流程。只有采用个性化的设置才可以提高产生系统的效率,增加经济效益,当前我国很多选煤厂都采用量体定做的形式。此外,选煤厂的高效还需要注重煤泥水系统和介质系统等,只有不断创新的工艺技术以及维护设备稳定安全运行才可在根本上增加选煤厂选煤的效率。
目前,选煤工艺设计向着工艺系统简单化,经济效益最大化的方向发展。对于选煤厂而言,小型化的厂房设计、基础建设投入的最小化、生产设备的最大化以及生产过程的智能化和自动化已经成为了现在选煤厂发展的主要趋势。因此,大量大型、高效、配套的选煤设备研制开始越来越重视先进技术的应用,开始不断的将新技术和新工艺融入到选煤工艺之中。
除了传统的煤炭洗选的工艺加工方法,新的深度加工煤炭的方法也不断出现,这也是选煤工艺发展的另一个特征。煤矸石发电技术、煤泥成型及煤泥发电技术等都是选煤技术研究应用到实践中的具体实例。在不远的将来,选煤厂可能会成为煤炭深度加工以及综合利用的综合性的生产单位。
我国是世界上第一煤炭生产大国,常规的选煤设计工艺上已达到成熟,但是随着市场的不断变化,应不断对选煤工艺进行改革创新,以适应新的市场变化规律。选煤厂在设计时应注重产品结构的定位,在工艺设计前,要全面分析煤质资料并且充分了解设备性能,从而使各个生产环节有机结合在一起,创造更大的经济效益。
选煤工艺是选煤厂的灵魂,它决定了选煤厂的生产规模、生产方式、生产成本、产品结构和经济效益。选煤工艺的设计应结合原煤的特性、用户对产品煤的质量要求、最大产率和最高经济效益以及选煤厂的建设规模、工艺环节设置等多个方面综合考虑。
西安煤业公司重介质选煤厂设计能力为0.6Mt/a,采用有压三产品重介质旋流器分选、煤泥浓缩、尾煤压滤脱水的工艺。该厂洗后精煤产品主要用于电厂动力发电,所以该厂工艺流程较简单,煤泥水处理系统、基建投资及加工费较低,既能提高煤炭加工效率又利于环保。
由于西安煤业公司六区矿井主要进行残煤回采,所以在开采煤层过程中,个别煤层夹矸煤较多,大量的矸石及夹矸煤进入原煤,使原煤矸石含量增大。为了满足电力用户需求,根据块煤和末煤粒度特性,该西安煤业选煤厂原煤采用动筛粗选-重介质旋流器精选的方式。该厂实现了重介质旋流器分选工艺产品下限低,洗选出的煤含煤泥量少,分选精度高,对煤质的适应性强,自动化程度较高的效果,该选煤厂工艺流程见图1。
块煤预筛的目的是排除原煤中大块矸石,该厂选择适用于不分级混合入选的预先筛分作业方式,既减小了破碎机的负荷,也减少了物料的过粉碎和提高了手选作业的效率。预先筛分筛孔尺寸为50mm,手选作业为检查性手选,破碎作业采用闭路破碎流程,破碎后产物再返回预筛分机进行检查性筛分。
由于该厂为中型选煤厂,所以采用一台有压三产品重介质旋流器即可满足生产需要。重介旋流器分选的精煤、中煤、矸石分别经各自系统的弧形筛、脱介筛、离心机脱介、脱水后,作为最终产品进仓储存。有压给料重介质旋流器的突出优势之一是有效分选下限低,重介质旋流器直径大小相同时,有压给料方式较无压给料方式处理能力高15%左右,此外有压给料所需介质循环量较少,入料压力较低。
由于该厂处于东北严寒地区,需将末精煤在离心脱水机中脱水,与块精煤一起进入精煤仓,最大限度地回收精煤。尾煤及高灰煤泥水采用浓缩、压滤处理,确保洗水闭路循环。由重介质旋流器二段排出的矸石经过直线振动筛进行收集,筛下末矸石经过预先脱水,排出厂房。
该厂采用直接磁选方式,设备种类少,缩短了循环介质的路程,流程简单尾矿中磁铁矿损失小;另外戒指的净化、回收过程滞留时间短。介质采用合格磁铁矿粉加水配置而成,由泵打入分选设备。系统中精煤预先脱介、分流,精煤脱介后的合格介质与矸石合格介质一起进入合介桶循环使用,稀介分别进入各自对应的磁选机净化回收。
矸石磁选尾矿经倾斜板浓缩机、矸石离心液由振动弧形筛及矸石脱介筛联合处理,分理处的振动筛筛下产物进入一段浓缩机,筛上产品掺入矸石。精煤磁选尾矿由振动弧形筛、一段浓缩机、煤泥离心机联合处理,分离出的末精煤产品掺入精煤;离心液与一段浓缩溢流共同进入二段浓缩机,浓缩底流进行压滤及干燥,得到干煤泥产品;二段浓缩溢流及压滤滤液进入清水循环统。系统采用加压过滤机对细煤泥脱水回收,产品水分低,根据发热量大小可掺入末煤或单独销售,并确保煤泥水闭路循环不外排。
选煤厂生产过程中原煤的数质量具有不均衡性,随时都可能产生波动。为保证选煤厂的正常生产,在设备选型时每个设备的选型依据应该是相对应作业环节的处理量乘以不均衡系数,若没有特定条件,不均衡系数的选取均应按GB 50359―2005《煤炭洗选工程设计规范》规定执行。综合考虑节能、使用寿命等因素,尽量选择同类型、同系列的设备产品,便于检修和更换。
厂房采用重选与压滤干燥车间联合建筑方式;厂房工艺布置中,遵循煤流简捷、顺畅,中转环节少,占地省的原则,以便缩小厂房体积,节省投资;厂房布置方式采用系统模块化、单层厂房大厅式,方便了设备检修;用钢结构代替常用的钢筋混凝土结构,使设备布置更方便,安装、调整更简单。
2010年3月哈密广汇年产120万吨甲醇/80万吨二甲醚(煤基)项目获得国家发改委正式核准。该项目是新疆广汇集团抓住国家实施西部大开发和能源结构调整战略的机遇,充分利用新疆哈密伊吾县丰富的煤炭资源和相对丰富的水利资源,而大力发展新型煤化工清洁能源产业的大背景下做出的战略性投资决策。该一期项目于2007年5月正式启动,计划到2010年底联动试车。项目采用先进、可靠的工艺技术生产甲醇/二甲醚、LNG,实现煤炭资源的清洁转化。项目包括:建设化工生产区、配套煤炭开发和库容为960万立方米水库等建设工程。具体建设内容为:4×600t/h 高压煤粉锅炉,3×50MW抽汽式汽轮发电机组,两套6万方空气分离装置,14台碎煤加压气化装置,四套低温甲醇洗装置,四套混合制冷装置,两套甲烷深冷分离装置,两套甲醇合成与精馏装置,两套二甲醚合成与精馏装置;建设先进的污水处理装置,实现废水零排放;建设先进的烟气氨法脱硫和湿法硫酸装置,为实现废物资源化利用奠定了基础。该项目关键设备与重要仪器仪表的选型采用国际知名品牌,遵循切实可靠与适度先进相结合;其他设备通过招标采用国内名牌产品;精甲醇产品达到美国AA级产品质量标准;二甲醚及LNG产品符合国家相关标准。
生产工艺及设备设施项目主工艺选用碎煤加压气化技术和国产化低温甲醇洗净化技术。甲醇、二甲醚合成、甲烷深冷分离及硫回收、空分等技术需要国外引进。技术来源是采用了德国林德空分技术、瑞士卡萨利甲醇合成技术、美国康泰斯/BV甲烷分离技术、德国TGE公司的LNG储罐、丹麦TOPSOE二甲醚合成与硫回收技术、赛鼎工程有限公司的碎煤加压气化技术与低温甲醇洗技术;南昌大学的酚氨回收技术等。
厂外煤经备煤、筛分,合格的碎煤送至气化,在碎煤加压气化炉中气化,粗煤气经煤气冷却及低温甲醇洗可以将大部分有害气体组分脱除干净,在低温甲醇洗出口净化气体中主要有CO、H2、CH4、N2、Ar以及0.1ppm的总硫和约20ppm的CO2。
分离甲烷后的净化气和低温甲醇洗分离的CO2经过合理的比例混合经合成气压缩机组压缩去甲醇合成生产出粗甲醇,粗甲醇精馏后得到中间产品精甲醇。
加压气化、煤气冷却分离的煤气水送至煤气水分离装置分离出焦油、中油、石脑油,剩余的含酚污水至酚回收、氨回收得到粗酚、液氨后废水送至生化处理。
液氨送至热电站和烟道气中的硫生产硫酸铵,烟道气达到规定的标准后排入大气。
低温甲醇洗分离出来的酸性气体在硫回收装置生产浓硫酸,尾气送至锅炉的烟囱。
1.2.1碎煤加压气化配套低温甲醇洗净化工艺碎煤加压气化产生的粗煤气成分复杂,包括CO、H2、CO2、CH4、H2S、有机硫、C2H4、C2H6、C3H8、C4H10、HCN、N2、Ar以及焦油、脂肪酸、单酚、复酚、石脑油、油、灰尘等。在这些组分中除CO、H2有效组分和CH4、N2、Ar以及烃类属惰性气体外,其余所有组分包括CO2和硫化物都是需要脱除的有害杂质,通过低温甲醇洗净化可在同一装置内全部、干净地脱除这些有害成分。
1.2.2“低压法”合成甲醇,气相甲醇脱水,间接法(两步法)制备二甲醚工艺净化后的煤气中的CO和H2经过化学反应合成甲醇,甲醇脱水可制取二甲醚。
“合成甲醇”与“甲醇脱水”反应是在一定压力、温度,且有催化剂存在的条件下进行的。该工程优选“低压法” 合成甲醇,是指操作压力在5~10MPa范围内进行反应,操作温度为210℃~260℃,典型的低压法工艺有国外的Lurgi、Topsoe和TEC等工艺。同时甲醇脱水反应选择了气相甲醇脱水法。
围绕以上选择的主要工艺技术,装置生产过程中先后经过备煤、加压汽化、煤气冷却、低温甲醇洗、、甲烷分离、合成气及循环气压缩、甲醇及二甲醚合成主工艺过程,相应的配套工程装置为热电站、空气压缩分离及氨吸收制冷、煤气水分离、酚回收、氨回收、硫回收、氢回收等辅助工艺。
(1)备煤流程。备煤系统的任务是为气化炉提供合格的原料煤以及锅炉提供合格的燃料煤,内容包括原料煤、燃料煤的卸车、上煤、贮存、粉碎、筛分及运输。
原煤由汽车卸进卸煤槽内,通过卸煤槽下部叶轮给煤机送入破碎厂房,将原煤破碎到Φ8mm的原料煤送到气化缓冲仓贮存,Φ
为确保气化炉正常生产,气化备煤系统在筛分厂房和入炉前的转运站中设置了弛张筛,以保证进入气化炉的原料煤Φ>
8mm。
(2)加压气化流程。碎煤加压气化装置由气化炉、加煤煤锁和排灰灰锁组成,并有洗涤器和废热锅炉与之配套。
当煤装满煤锁后,充压至气化炉的操作压力后加入气化炉。蒸汽、氧气混合物作为气化剂,经旋转炉蓖喷入,与上升气流逆流接触。煤经过干燥、干馏、气化和燃烧层、灰层后,残留灰由气化炉中经旋转炉蓖排入灰锁,再经灰斗排至水力排渣系统。
煤锁用来自煤气冷却装置的粗煤气和来自气化炉粗煤气分两步充压,卸压的煤气收集于煤锁气气柜,由煤锁气鼓风机送往燃料气管网。减压后,留在煤锁中的少部分煤气,用喷射器抽出,经煤尘旋风分离器除去煤尘后排入大气。
在此过程中,灰锁也进行充压、卸压的循环。为了进行泄压,灰锁接有一个灰锁膨胀冷凝器,逸出的蒸汽在水中冷凝并排至排灰系统。
离开气化炉的煤气进入洗涤冷却器,洗涤并使其饱和后的进入废热锅炉,通过生产0.5MPa(表压)低压蒸汽回收部分煤气中蒸汽的冷凝热,在废热锅炉下部收集到的部分冷凝液用洗涤冷却器循环泵送出。多余的煤气水送往煤气水分离装置。离开气化工段的粗煤气通过粗煤气总管进入煤气冷却工段。
第一步, 181℃的粗煤气进入粗煤气洗涤器,大量灰和少量焦油被洗涤下来,温度下降2℃~3℃。分离器顶部出来的粗煤气进入预冷器A/B,从179℃冷至140℃,其中部分焦油和水蒸汽将冷凝下来。
第二步,在中间冷却器A/B中,粗煤气由140℃降至70℃,煤气中部分油和水蒸汽将冷凝。粗煤气从中间冷却器的管程顶部进入,底部排出。冷却介质为脱盐水。
第三步,粗煤气在最终冷却器中由70℃降至37℃,此时冷凝下来水蒸汽和少量的油。煤气仍是从最终冷却器管程顶部入,底部出。冷却介质为循环冷却水。
第四步,从最终冷却器出来的粗煤气进入最终分离器,除去夹带的少量液滴,得到的粗煤气进入低温甲醇洗工段。
(4)低温甲醇洗流程。来自煤气冷却工段的粗煤气进入H2S吸收塔底部的预洗段以除去粗煤气中的高分子烃类(石脑油)和其它诸如有机硫、HCN和NH3等微量组分。预洗甲醇富液加热后到预洗闪蒸塔闪蒸解吸,预洗后的粗煤气进入H2S吸收塔的脱硫段,脱硫后进入CO2吸收塔。
在CO2吸收塔中除去粗煤气中的CO2、微量H2S和COS等硫化物,使煤气中CO2≤20mL/m3、总硫≤0.1ppm送入合成压缩机。来自CO2吸收塔的富CO2甲醇富液进入CO2闪蒸塔的Ⅰ、Ⅱ、Ⅲ段进行闪蒸和Ⅳ段气提脱除CO2得到含5.1% CO2的甲醇半贫液,其中Ⅰ段闪蒸汽到换热器复热后作为燃料气送出界区,Ⅱ段闪蒸和Ⅳ段气提气送到尾气洗涤塔,Ⅲ段脱除的98% CO2送到甲醇合成工段。
来自H2S吸收塔的含硫甲醇富液进入H2S闪蒸塔脱除气体中的H2S和COS后,送往二氧化碳尾气洗涤塔。
H2S浓缩塔Ⅱ段的富硫甲醇液进入热再生塔再生后得到的贫液甲醇,经富/贫甲醇换热器冷却后,送到CO2吸收塔顶作为精洗甲醇液。
(5)氨吸收制冷流程。来自低温甲醇洗装置的气氨经氨压缩机加压0.3MPa(a)后,再被稀溶液吸收,送入吸收器,被溶液吸收,成为39℃、52%的溶液,经泵加压到2.3 MPa(a)后送到精馏塔,精馏出的氨气浓度大于99.8%,温度为55℃,进入氨冷凝器后被冷却水冷凝为40℃的液氨,再经过冷器过冷为5℃,1.78 MPa(a)液氨,送往低温甲醇洗各氨蒸发器。
(6)煤气水分离流程。从煤气冷却工段来的含油煤气水与低温甲醇洗来的煤气水经冷却器后进入含油煤气水膨胀槽,减压释放出蒸汽和溶解气体。
膨胀后的煤气水流入油分离器,溢流出的油送至罐区。加压气化来的含尘煤气水与煤气冷却工段来的含焦油煤气水送往初焦油分离器分离出尘-焦油-水混合物,进入粉碎器粉碎后经循环泵送至气化炉。分离出的膨胀气经冷却后,送硫回收装置。煤气水送往酚回收装置。
(7)酚回收流程。从煤气水分离来的酚水经过脱酸塔底酚水换热器预热后,送入脱酸塔分离出酸性物质CO2 、H2S。而后酚水与二异丙基醚液―液萃取,将酚萃取出来,通过加热将其中的异丙基醚和氨分离出来,得到粗酚。
(8)氨回收流程。从酚回收工段来的含CO2、H2S的氨水经氨水预热器预热后进入汽提塔,净化、汽提后进入氨冷凝器,冷凝后的汽液混合物在氨汽液分离器中分离,液相返回汽提塔作为回流液。气相进入提纯塔,在吸收器中形成25%的氨水,然后进入精馏塔得到液氨,送到全厂罐区
(9)硫回收流程。本装置采用托普索WSA湿法硫酸工艺。酸性气在燃烧炉中燃烧生成SO2工艺气,炉温约1000℃。在SO2反应器内工艺气催化、氧化生成SO3,再经冷却、转化,在WSA冷凝器冷凝生成246℃、浓度约98%热硫酸,从底部排入酸槽,降温至70℃后经酸泵送至酸冷却器冷却至40℃,一部分做循环酸用,一部分作成品酸送至界外硫酸储罐。冷凝分离后的尾气送至烟囱放空。
(10)甲烷分离流程。原料气进入冷箱中经过换热器被冷却到约-157℃,经分离罐分离成气―液两相。汽相经膨胀机制冷至-171℃后与液相进入精镏塔进行分离、精馏,节流减压后得到液态CH4产品。其中冷却工艺采用液氮节流膨胀制冷和冷剂压缩节流膨胀制冷和膨胀机制冷。
(11)合成气及循环气压缩流程。来自低温甲醇洗工序的常温常压CO2用CO2压缩机加压至约2.4MPa,送到甲醇合成与来自深冷分离工序的新鲜合成气混合进入合成压缩机加压至约4.1MPa,在缸内与合成来的循环气混合再增压至约8.5MPa后,送到甲醇合成系统。
(12)甲醇、二甲醚合成流程。来自甲烷深冷分离的新鲜合成气,补入来自氢回收单元的氢气和来自低温甲醇洗的CO2后,氢碳比满足甲醇合成的要求,经合成气压缩机进行二段压缩,再经气/气换热器预热到215℃后,进入甲醇合成塔,在催化剂的作用下进行甲醇合成反应 :
甲醇合成塔为副产蒸汽型等温反应器。合成塔出口气进入气/气换热器与合成塔入口气换热,温度降至120℃左右。出气/气换热器气体后,再经空冷器和水冷器冷却到40℃,进入甲醇分离器进行气/液分离。出甲醇分离器气体大部分作为循环气去合成气压缩增压并补充新鲜气,一小部分为弛放气,送往氢回收装置;从甲醇分离器分离出来的粗甲醇通过粗甲醇过滤器,除去石蜡、催化剂粉尘等固体杂质,经分离器液位调节阀减压至0.5 MPa(g)后,送至闪蒸槽,释放出溶解气体。粗甲醇送至甲醇精馏,贮罐气则送燃料气系统。
来自甲醇罐区的原料甲醇经过甲醇预热器加热后,送至甲醇蒸发器,通过中压蒸汽加热蒸发,再与二甲醚反应器出口物料进行换热,升温进入二甲醚反应器。
反应器中约80%的气相甲醇脱水生成二甲醚。从反应器出来的这股物流在送往二甲醚精馏段之前通过进出物换热器、甲醇塔再沸器及甲醇预热器使其冷却。之后通过循环水在二甲醚反应物冷却器中再次冷却。然后经二甲醚分离器分离,送入二甲醚塔精馏、抽出二甲醚后,送至二甲醚罐区。
(13)氢回收流程。由甲醇合成工序来的8.3MPa、40℃的弛放气经洗涤、分水、加热后,进入膜分离器。在膜两侧气体组分分压差的驱动下,弛放气中的H2、CO、CO2等气体选择性通过膜壁,在膜分离器低压侧得到的压力为2.4MPa的富氢气,经冷却至40℃后去合成气压缩机,膜分离尾气去燃料气管网。
(14)空气压缩分离流程。原料空气经过滤、压缩、冷却、洗涤后,再经吸附除去水分、二氧化碳、碳氢化合物的纯化过程,得到洁净工艺空气。
净化空气一股经冷却、一次分馏。其余部分经增压、增压、膨胀制冷后,参与精馏。另一股经继续增压、冷却、液化后,参与精馏,得到氧气、氮气。副产物污氮经升压、复热后,作为分子筛再生气,另外进入水冷塔冷却循环水。
哈密广汇一期煤基项目总投资67.5亿元,经济服务年限15年,产品成本具有较强的竞争力,盈亏平衡点27.8%,抗风险能力较强,全投资内部收益率23.7%,投资回收期(税后)6.39年(含3年基建期)。它以煤为原料,生产甲醇、二甲醚等石油替代产品,弥补地区对液化石油气等石油产品需求的不足。项目采用国际先进技术、优化生产工艺以及加强能源利用等措施,使每吨二甲醚综合能耗达到2.62吨标煤,并加大煤渣综合利用、水资源节约及和二氧化碳减排工作力度,积极创造条件,实现废弃物零排放。项目建成后,可以将生产中伴生的甲烷等有效气体分离成液态甲烷和其它副产品,最终实现煤炭资源的清洁转化。与国内同类装置相比,这一项目属煤炭洁净高效生产系统,是煤炭综合利用,提高附加值的最有效、最经济途径,技术达到国际先进水平、工艺成熟,能量转化率高,CO2排放量低,因此被国家发改委列为全国煤化工示范项目。
浮选工艺是指利用矿物表面所含杂质对于水的相溶性差异而采用强化的措施,使得其密度差达到一定的分离要求,使得杂质上浮而目的产物下沉的过程。所以在选煤厂的泥水煤分离作业中是得到广泛的运用的。在国内的相关产业里,浮选的技术是最成熟的,对于矿浆到精煤的过渡的产率也相对是最高的。但是随着原煤中的细泥含量的不断增加,浮选作业的难度也在不断增加,所以对于浮选工艺和浮选剂的进一步发展就提出更高的要求。本文以分析选煤厂的浮选工艺和浮选药剂的发展为线索,对于浮选工艺和浮选剂的发展和应用进行一定程度的探讨。
对于不同粒级的煤泥进行的分离,在浮选的速度和纯度上有着较大的差异。所以在浮选的工艺上主要采用的分级的浮选过程。选煤厂主要采用的就是这样的一个工艺流程,首先是精煤磁尾桶将原煤进行了磁力分选得到了含有细泥的原料,在运用分级旋流器和弧形筛的二级分选作用,得到了浓缩池中的原生煤浆,再将泥浆用泥浆准备器储存,分批进入浮选机进行浮选,出品经过加压过滤机,一部分合格精煤运出,一部分回流浮选机再次浮选,达到预想指标,减轻机器的负担。这个工艺流程可以说是十分完善和规范的一个工艺流程。
分级旋流器和弧形筛的结合是对于浮选工艺的一大进步,这就像是一个筛网旋流器一样。首先是分级旋流器通过水力作用,使得密度大的颗粒物沉降,密度小的和煤粉一起存在于液相中由上口排除。这种操作即可达到预想的对于粗粒级、中等粒级和高灰细煤的一个初步的分离效果了。旋流器主要的工作原理还是针对于密度差而言的,在其中心部位会形成二次涡流从而使得粗级和细级颗粒的分离。接下来就是进行连续作业的弧形筛,弧形筛作为筛网中的一种效果比较好的型号,在进行筛分的时候,会尽量使得筛上物和筛下物的比例恒定于需要的范围内。这就相当于在旋流器的步骤是对于粗细颗粒的分离,而这个步骤是对于细中颗粒的分选,这样的结果就使得最终得到的原煤浆的杂质含量大大降低了,减少了对于后续处理的难度和机器的损耗。这个工艺流程环节主要的效益有如下几点:(1)首先是针对于产品的质量、价格和成本。成本虽然要比以前的工艺流程提高少许,但对于机械的保养费以及产品的质量都是一种促进的作用,是有很大的经济优的。(2)重选和浮选的原料合格,对于后续的工作而言,前处理的产物所含的粗颗粒越少越好。
对于从预处理而来的原煤浆,首先是进行的重力分选,也就是离心机针对于离心力的差异将密度较大的颗粒物分离出去,通过这个环节达到浮选环节的初产品就是很好进行浮选的了。流程的具体确定是以煤泥的性质和煤化程度的深浅来确定的,所以在浮选的终环节的产品回流工艺是很好的处理方式,这样既可以减轻设备的负荷也可以使得产品精度提高,也是事故的一种处理方式。
首先就是浓缩池的运用,对于从上一阶段的分级旋流所得到的产品而言,这一步的进行可以说是浮选工艺的革新,对于前处理的分选过程,对于三级颗粒的分离到了这一步可以说已经很完备了。进行浓缩效应,对于原浆含水率的降低起到了很大的作用,也可使原料混合均匀。
浓缩池进行浓缩之后的环节就是主要的核心环节,对于浮选的过程而,浮选药剂的选用是十分关键的,另外还有水力停留时间的设定也很重要,对于不同的季节时令,水温的差异也要考虑。这个环节还包括压滤机对于精煤浆的脱水处理,在脱水之后的产品再进行灰分的测量,对于不合格的产品进行回流处理,最终使得获得的精煤产品达到预设的纯度。
这个环节的工艺流程主要的特色就是分级浮选。对于浮选而言,涉及到的主要的影响因素就是原料中的固体颗粒的含量,还有产品的纯度和回流问题。在这个离心和回流相结合的分级处理的过程中,就使得浮选的工艺流程更加成熟完善。
对于浮选工艺而言,选煤厂的分级处理工艺流程是很成熟的,对于产品的质量也是有保障的,在浮选的过程中的成本控制也比较到位,对于浮选工艺的革新是很有帮助的。
浮选药剂是指在浮选进行的初期,加入的化学试剂,针对于有密度差的颗粒物和成品组分而言,增加疏水颗粒的疏水性,使得其能够与起泡剂作用下的空气泡一起上浮在水面成为浮精,而目的组分在水中形成煤泥。浮选剂的作用主要是提高煤粒表面疏水性和煤粒在气泡上粘着的牢固度;在矿浆中促使形成大量气泡,防止气泡兼并和改善泡沫的稳定性,使煤粒有选择性地粘着气泡而上浮;调节煤与矿物杂质的表面性质,提高煤泥的浮选速度和选择性。
起泡剂的定义是能够促进泡沫的形成,增加分选界面的药剂。起泡剂为了使颗粒物的密度急剧减小,缩短浮选时间,所以采用起泡剂使得水中的空气泡的数量增多,是颗粒物疏水端和气膜接触,形成很大的一个絮团,通过重力自由沉降的过程浮于水面。所以起泡剂的种类选择是是很重要的,选煤厂选用的是杂醇作为起泡剂,首先除了乙醇外,其他的醇是难溶于水的,所以采用杂醇作为起泡剂首先就疏水性的增强起到的一定的作用,再就是由于其密度一般比水大,粘度也较大,这样气泡就很容易形成。可以在很短的时间达到预想的泡量。所以对于起泡剂的用量也是需要控制的,使得溶液呈现一种乳化的状态时最有利。使用价格较低的工业杂醇,就这个乳化的作用而言也是很好的。
捕收剂是指是目的颗粒表面疏水,增加可浮性,使其易于向气泡附着的浮选药剂。和起泡剂的协同作用使得浮选的过程更加便易,这是捕收剂的主要作用所在。在浮选工艺中,捕收剂的作用是不容小觑的。针对于近年来捕收剂的发展,就选煤厂而言,选用柴油作为捕收剂是很好的一种发展和应用。首先柴油和水是不互溶的,增加了其可浮性,并且相对于其他的化学捕收剂柴油的污染较小,回收处理方便,重复利用性高,是很不错的选择。
对于浮选工艺和浮选剂的发展和应用,通过对于选煤厂的工艺流程和药剂选择的分析,可以看出,采用分级浮选,将前处理进行步骤化的效果是很好的。而对于浮选剂的选择,主要考虑到的是经济效益和环境效益。
[1] 赵宏馨.重介质旋流器分选煤泥技术现状及今后研究方向[J].洁净煤技术,2006,12(2);28―30.
如今不论是技术方面还是经济方面,都为煤转化技术生产取代石油燃料和化工品提供了有利条件。随着天然气和石油能源供应的日趋紧张,煤化工能源将会发展成为化工原料的主流。褐煤发展煤化工的优势:第一,我国褐煤资源丰富,而且褐煤成本低下。在我国的很多褐煤地煤田,煤层都较浅,开采起来比较简单,甚至有些地方还可以进行露天开采。因此褐煤的产出效率高,安全性高,成本较低。第二,有成熟的煤化工技术做后盾。相对来讲,褐煤还属于一种比较年轻的资源,不存在明显的粘结性,而且化学性质活波,非常有利于实现综合加工和能源转换。当前应用较广泛的煤化工技术有以下几种:1.热解提质技术;2.煤的气化技术;3.煤的液化技术。第三,产区环境容量和水资源的有利条件。水是实现煤化工技术必不可少的条件,而出产褐煤的地方往往都是水资源丰富的边远地区,环境地广人稀,是进行大规模煤化工基地建设的最佳位置。因此,开发以褐煤为原料的煤化工工艺技术成为现代煤化工的一种新的趋势。
煤化工就是利用多种化学加工技术把各种原料煤转化为液态燃料、气态燃料、固态燃料或者是化学品的工艺技术。我国褐煤资源丰富,再加上褐煤自身的多种资源优势,将会在煤化工应用中得到广泛应用。常用的褐煤煤化工技术包括褐煤的热解提质技术、气化技术以及褐煤液化技术。
褐煤的热解提质又称干馏提质,是指对褐煤在非氧化环境下或者隔绝空间的情况下进行加热,最后得到煤气、焦油和半焦(又称蓝炭)。褐煤经过热解后得到的煤气可以作为燃料用气,半焦具有固定碳高、低硫以及低灰的特点,在各种化工产业中的应用广泛,如可作为进行活性炭生产的原料、化肥、铁合金以及电石等行业的燃料等等。经热解后的褐煤失去了大部分水分,但仍百分之十的挥发分,其热值得到很大提高,不再容易发生挥发和自燃,有利于进行长途运输,此时可作为电煤使用。因为褐煤不存在粘结性,没有胶质层,经热解后得到的低温煤焦油和重油的性质及组成十分相近,具有很大的利用价值,如果经过深加工可以获取具有更高经济价值的酚类化学品。煤的热解提质工艺有很多种,在加热方法、加热速度、热载体类型等方面的技术要求都不相同,当前的热解提质工艺技术主要有褐煤固体热载体法快速热解技术和褐煤低温干馏改质技术。其中延长石油集团正在开发的CCSI技术就是低温干馏改质技术的典型代表。
褐煤的液化技术主要可以分为两种,直接液化工艺技术以及间接液化工艺技术。直接液化:在催化剂以及氢气的作用下,把煤经过加氢裂变反应后转换成为液态燃料称为直接液化。煤的直接液化工艺技术涉及到很多环节和流程,包括原料煤干燥过程、原料煤破碎过程、煤浆制备过程,到最后的态产物分馏以及精制加工过程。利用煤的直接液化技术可以生产出优质的液态石油气、汽油、柴油以及氨和硫磺,而且还可以进一步萃取出炭素、二甲苯等化工原料。褐煤的液化活性较高,因为其相对来讲碳含量较低,氢和碳的比例较高,结构中的羧基、氧桥、羰基以及亚甲基比较多,所以褐煤非常适合进行直接液化的。直接液化技术的典型代表有悬浮床加氢裂化技术(VCC),该技术最早起源于1913年德国Bergius-Pier煤液化技术,是通过煤化工与炼化的有效结合实现的。经过长期以来的不断改进和完善,全球首套VCC装置已于2015年初开车成功。VCC技术可以适用于塑料、低阶褐煤、劣质重油以及减压渣油等多种原料或者混合物。间接液化:先把煤气化成氢气和一氧化碳等气体,然后在一定压力和温度环境下利用煤基合成气原料将其催化转化为烃类燃料油的技术过程叫做间接液化。该技术方案主要基于煤气化工艺的产物,在催化剂作用下将合成气中的一氧化碳和氢气转化为石脑油,柴油等油品。目前F-T合成技术是间接液化的主流工艺技术。
煤炭液化以及其他煤化工应用的基础技术就是煤的气化技术,煤气化技术是进行煤化工生产和能源转换的主要途径之一。煤气化工艺技术是指在一定的压力和温度环境下,通过对水蒸气、氧气、空气等气化剂的作用下加热煤炭,煤炭经过受热发生分解,煤中含有的炽热的碳转化为游离碳,此时这些分解出来的游离碳和气化剂中的游离的氧、氢和碳进行有机结合,最终成为氢气、一氧化碳以及甲烷等可燃性气体。采用的气化剂不同的情况下就会形成不同热值的煤气。另外,煤的挥发分的差异也会给反应速度和产量造成直接影响。相比之下,褐煤的挥发分要低于具有较深变质程度的烟煤以及无烟煤,所以褐煤在进行气化的过程中反应活性特别强,反应速度快、无粘结性、气体产量高,是具有较大使用价值的的气化用煤。当前,褐煤气化在我国的化工产业中得到了广泛应用。煤的气化不同于热解,煤的热解过程只是把煤自身不到百分之十转化为可燃气体混合物,而气化过程则是把煤所包含的所有碳气化成为气态。相比直接燃烧褐煤进行气化表现出极大的优越性,因为气态燃料的燃烧相对比较稳定,没有环境污染,而且燃料的净化和运输都非常的方便,原料的配料控制简单,很大程度上简化了生产设备和生产工艺。另外,气态燃料能够适用于非均相催化的化工合成过程,而且气化过程中得到的灰渣也有多种用途,如可以用来制造肥料、水泥、砖瓦、土壤改良剂以及绝热材料等等。西门子的GSP气化技术:西门子的GSP气化技术是目前一种比较成熟的气化技术,至上世纪八十年代之间已有三十多年的研发经验,应用于煤化工也有二十多年的实际生产经验。西门子的GSP气化技术属于一项气流床气化技术,该技术过程包括的主要工艺流程有干粉进料、纯氧气化、液态排渣、粗合成气激冷工艺流程等。西门子的GSP气化技术的适应范围特别广,如褐煤、无烟煤、石油焦等等。该技术的气化温度通常在1350-1750摄氏度,而且碳转化率高达百分之九十以上。利用西门子的GSP气化技术可以把一些直接燃烧会造成较大污染以及一些比较廉价的煤、垃圾或者是石油焦转化为具有高附加值的清洁的氢气和一氧化碳。氢气和一氧化碳是化工产品生产过程中的基本原料,可以用于合成油、合成氨以及甲醇等化工产品的生产,另外也可以直接应用于城市煤气或者用于发电。
块煤(>50mm粒级)预分选的目的是排除原煤中的大块矸石,从根本上解决人工手选劳动强度大的问题。煤质好时,入选原煤可不进入主厂房分选,经过排矸后直接作为外销产品。对于可选性为易选的原煤而言,动筛跳汰排矸和重介浅槽排矸两种方法均可选用,但两者在实际使用过程中存在差异。动筛跳汰机主要用于排除大块煤中的矸石,具有工艺简单、用水量少、生产成本低的优点,但该设备有效分选精度低于重介浅槽分选机,且存在矸石带煤问题。重介浅槽分选机是利用煤和矸石密度不同使其在相对静止(非脉动水流)的重介悬浮液中分层的设备,由于重介浅槽分选机分选过程中煤和矸石在悬浮液中停留时间很短(大约是普通跳汰机的1/5~1/8,动筛跳汰机的1/2~1/3),且煤和矸石在设备内运动十分平稳,可以认为是相对静态分选,因此煤和矸石在悬浮液中很少相互挤压摩擦,最大限度地提高了设备分选精度,减轻分选作业中产生的次生煤泥量,所以该厂选用浅槽分选机对块原煤进行预分选。>50mm粒级块原煤采用重介浅槽分选机预分选,当煤质较好时,预分选后的产品即可满足市场需求,直接作为产品;当煤质较差时,预分选后的产品采用无压三产品重介旋流器分选+煤泥浮选的联合工艺分选。
当煤质较差,预分选后的产品达不到质量要求时,需对<50mm粒级原煤进行再选。由于入选原煤为稀缺煤,为了最大限度地提高精煤产率和经济效益,需要对煤泥进行分选,即末煤的分选下限为0mm。富城矿业选煤厂原煤筛分试验结果如表1所示。由表1可知,入选原煤中6~3mm粒级产率为14.03%,3~0.5mm粒级产率为27.48%,<0.5mm粒级产率为13.51%,细粒级含量较高。若采用跳汰分选工艺,物料透筛严重,在分选过程中势必造成大量精煤损失;若采用有压三产品重介旋流器分选工艺,原煤在悬浮液中浸泡后经离心泵叶轮撞击和管道运输,必然产生大量煤泥,煤泥含量的增高将导致综合精煤产量降低,生产成本增加。故采用无压三产品重介旋流器对50~0.5mm粒级原煤进行分选。
针对入选原煤煤质多变的特点,该厂采用对煤质波动具有很强适应能力的机械搅拌式浮选机对细煤泥(<0.5mm)进行分选。机械搅拌式浮选机双层伞形叶轮、定子及假底上的稳流板组合有利于浮选,槽内下部的剧烈搅拌可促进气泡矿化;上部液面平稳,能加强精煤二次富集,有利于提高设备处理能力和浮选选择性。喷射式浮选机是一种微泡浮选设备,由于循环泵叶轮的猛烈搅拌、喷射乳化,充气煤浆高速撞击器壁后气泡粉碎程度较高,不利于气泡矿化,常出现尾煤灰分偏低的情况,因此该设备不适合对细煤泥浮选。由于该厂原生煤泥含量较高,为简化工艺流程,末煤分选采用选前不脱泥无压三产品重旋流器分选+机械搅拌式浮选机浮选的联合工艺。
(1)原煤准备。入选原煤经筛分、排矸、破碎后,>50mm粒级块煤由重介浅槽分选,浅槽精煤脱介、脱水后破碎至50mm以下,与筛下脱水末煤一起由带式输送机运至原煤仓,矸石产品脱介、脱水后作为最终产品进入矸石仓。原煤仓内的产品既可作为商品煤外销,也可由带式输送机运至主厂房由无压三产品重介质旋流器分选。
(2)主选工艺。重介旋流器分选的精煤、中煤、矸石分别经各自系统的弧形筛、脱介筛、离心机脱介、脱水后,作为最终产品进仓储存。精煤部分的煤泥水回收粗煤泥后进入浮选机浮选,浮选机采用3+2布置形式(煤质好时,开前3室即可;煤质不好时,5室全开)。当中煤部分的煤泥水灰分达到入浮要求时,将这部分煤泥水与精煤部分煤泥水一并处理,以增加综合精煤产率。
(3)产品脱水脱介。重介分选后的产品进行预先脱介及脱介、脱水、分级,考虑到脱介、脱水、分级效果,脱介筛均采用相同处理能力中长度较长的设备。筛下物料采用先进的卧式振动离心脱水机脱水,浮选精煤采用卧式沉降过滤离心脱水机和快开压滤机联合脱水,最大限度地回收精煤;浮选尾煤及高灰煤泥水采用浓缩、压滤处理,确保洗水闭路循环。
(4)介质添加及回收。介质采用合格磁铁矿粉加水配置而成,由泵打入分选设备。块煤系统中精煤预先脱介、分流(通过调节分流量确保介质循环系统的稳定),精煤脱介后的合格介质与矸石合格介质一起进入合介桶循环使用,稀介与矸石稀介一起进入磁选机净化回收;末煤系统中精煤同样预先脱介、分流,精煤、中煤、矸石脱介后的合格介质进入合介桶循环使用,稀介分别进入各自对应的磁选机净化回收。
(5)粗煤泥回收。精煤磁选尾矿由分级旋流器、振动弧形筛、煤泥离心机联合处理,产品掺入精煤;块煤磁选尾矿及中煤磁选尾矿由分级旋流器、高频筛联合处理,产品掺入中煤;矸石磁选尾矿及矸石离心机离心液由振动弧形筛及矸石脱介筛联合处理,产品掺入矸石。当只开块煤系统时,块煤系统的粗煤泥可由块煤系统的分级旋流器、振动弧形筛、煤泥离心机联合处理。
(6)工艺布置。原煤准备车间采用阶梯形布置形式,各工艺设备间衔接紧密,生产管理方便;主厂房采用大厅式布置形式,脱介筛、压滤机、浮选机等大型设备均布置在同一层,统一由大型桥式起重机提升,设备吊装、检修方便。
富城矿业选煤厂工艺流程具有“设计合理、技术先进、系统可靠、灵活高效、整体配套、管理方便”的特点,具体如下:(1)工艺流程和环节设置先进、合理、可靠。设计采用先进的重介分选技术,大大提高了分选精度和分选效率,浮选机采用3+2布置模式,可适应不同煤质的要求,煤泥回收环节高效可靠,有效遏制了“跑粗”现象。(2)充分考虑了入选原煤煤质波动的问题及当地煤炭市场供需情况,原煤既可单纯由重介浅槽排矸,又可进入主厂房全级入选;在煤质较好时,能够确保大块原煤的分选效果,简化了工艺流程。(3)主要设备技术先进、生产可靠,保证了分选、分级、脱水、脱介效果,提高了系统可靠性和高效性;各工艺设备衔接紧密,生产管理方便,厂房内的大型设备均可采用桥式起重机提升,设备检修、维护十分方便。(4)原煤分选、产品脱介脱水、介质回收、粗煤泥回收、浮选精煤脱水、浮选尾煤压滤等环节采用自流形式,工艺布置紧凑,中间转载环节少,既节省了空间,又降低了能耗。(5)地面工艺系统布局合理、布置简洁,煤流顺畅,功能分区明确,能够满足选煤厂大规模生产的要求,并充分考虑了全厂的安全生产。
这类污染物的主要来源是煤炭储仓、粉煤气化储仓及煤粉制作环节上产生的粉尘,在上述储仓的顶端排放点应该设置高效袋式除尘装置。除尘装置收集到的煤尘应该尽可能回收到储仓以提高利用效率。在废气高空排放时必须符合排放标准,废气含尘浓度不能超过120mg/m3。
为了保障生产装置运行的稳定、现场员工的生命安全以及尽可能的保护化工企业周围环境,通常会设置火炬装置,在生产开车、日常运行、紧急停车和事故处理时流程中产生的无法回收以及有毒有害的气体污染物进行燃烧处理。煤制甲醇工艺流程中气化装置刚开车后制备的煤气后系统不能及时的接气,产生的这部分气体通常都通过火炬燃烧进行处理,而且在生产稳定后一旦发生生产事故也能够将气化装置生产的煤气通过火炬燃烧出来,待解决了生产事故后在接气生产。工艺废气还可以通过燃烧和换热进行体系内的换热循环。例如对于甲醇合成工艺流程的尾气、甲醇精馏环节回收的不凝气,其主要包括H2、CH4、CO、甲醇等。通过这些废气燃烧,为将热量送至整体的换热网络供其他用户使用。煤质甲醇生产中硫回收装置可以同时回收硫磺成品,通过把净化工段收集到的硫化氢气体进行处理,尽可能的回收硫,以保证尾气能够达标排放。
煤气化是煤制甲醇工艺中不可或缺的重要工艺,对于不同的煤气化工艺,产生的污染物无论是种类还是数量都有较大的差异。为了提高甲醇生产企业对于水资源的重复利用效率,绝大多数的煤制甲醇企业都将其工业废水的循环使用作为了工艺设计的重点,在降低水资源消耗的同时,也降低了污水处理系统的处理负荷。可以合理的在工艺中引入预处理系统,先在体系内部循环,再进行污水处理。例如在德士古水煤浆气化工艺中通过灰水处理装置的运用,能够将气化过程中收集的黑水通过闪蒸、沉降、压滤等工艺的处理,将绝大多数的灰水回收利用,仅将很少一部分的污水送至污水处理体统中;煤气冷凝液,能够被用来洗涤煤气。利用污染物质含量低的新鲜水与循环水,减少污水系统里污染物的含量,排放污水通过换热器将潜热回收后,进入生化污水处理装置进行净化,以满足排放标准;气化工艺污水、甲醇装置污水和生活废水同直接进入污水处理装置,完成净化处理后再进入循环体系回收利用。鉴于煤制甲醇工艺污水中氨氮含量较高实际情况,结合目前行业内对于氨氮废水处理的有效方法,绝大多数的煤制甲醇生产企业都采用了预沉降+SBR+多介质过滤工艺。SBR生化净化工艺流程较为简单,处理效率高、占地面积小。此外,使用效果好,处理时间快,净化后的水质佳。并且能够根据不同工段的工艺条件,灵活的进行调整;最后,这种方式对于氮、磷物质的脱除效果好,且不易产生污泥膨胀,便于污水的循环利用。
与废水、废气相比,废渣等固体污染物对于人员以及设备的危害程度相对较低,只需要及时将污染物进行清理避免对土地资源的长期占用。在废渣存放时,应该用布遮盖污染物,避免由于天气原因造成的扬尘,影响厂区的空气质量。煤制甲醇生产中会使用到一些含贵金属催化剂废渣。应该将这些废渣收集起来返回至生产厂家回收利用。对无法加以回收利用,有具有危险性的废渣,需委托具有危险污染物处理资质的企业进行处置。
综上所述,用煤炭为基本原料制备甲醇的工艺,生产流程十分复杂,并且各个环节中产生的污染物种类也很多,只有切实研究污染物的基本类型和来源,有针对性的采取合理有效的污染物防治措施,一方面能够将甲醇生产过程中产生的污染物排放控制在合理的范围内,保护了化工企业周围环境;另一方面通过对污染物的治理也能够提高热量和物料的回收利用率,提高了企业生产中的经济回报。
[2]罗刚,张文耀,邢艳萍.煤制甲醇工艺废水改造[J].黑龙江科技信息.2011(23).
[3]曹金胜,张兴无,翁希旭.煤制甲醇装置水治理工作经验总结[J].科技资讯.2011(29).首页,「博悦注册」,首页!